
Ce este Lean? Afla ce inseamna Lean Manufacturing si care sunt principiile si beneficiile acestei metodologii
Lean, cunoscut si sub denumirea de Lean Manufacturing, este o metodologie care se concentreaza pe eliminarea risipei si cresterea eficientei, cu scopul de a adauga valoare pentru client. Aceasta valoare este generata prin activitatile care transforma un produs din stadiul sau initial in forma finala solicitata de client, pentru care acesta este dispus sa plateasca. |
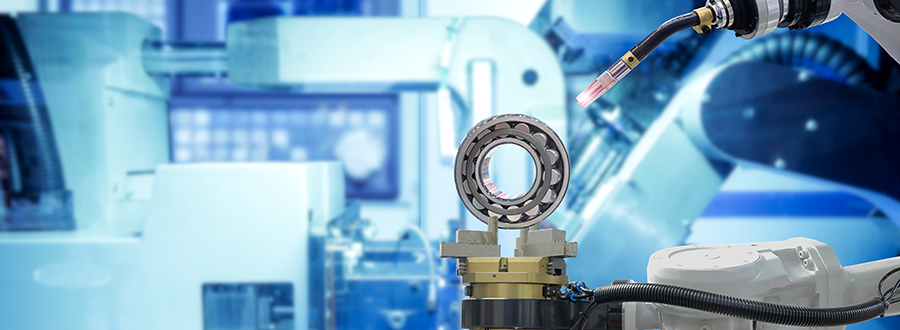
Ce este Lean Manufacturing?
Lean Manufacturing este o filozofie de management al productiei care isi are originea in Japonia si este centrata pe minimizarea risipei in toate procesele de afaceri. Conceptul a fost dezvoltat initial de Toyota si este cunoscut sub numele de Toyota Production System.
Principiile Lean se concentreaza pe imbunatatirea continua si pe eliminarea activitatilor care nu adauga valoare, cunoscute sub numele de „muda” in japoneza. Acest proces include, printre altele, reducerea timpilor de asteptare, miscarilor inutile, productiei excesive si defectelor. Imbunatatirea continua, cunoscuta sub denumirea de Kaizen, presupune efectuarea de modificari progresive ale proceselor pentru a spori eficienta, calitatea si satisfactia clientilor.
Ce inseamna Lean Management?
In centrul managementului Lean se afla conceptul de adaugare de valoare din perspectiva clientului. Acest lucru inseamna ca o companie va intelege ceea ce apreciaza cu adevarat clientii si va alinia procesele pentru a oferi aceasta valoare in cel mai eficient mod posibil. Concentrandu-se pe nevoile si preferintele clientilor, organizatiile isi pot optimiza operatiunile si pot elimina activitatile care nu contribuie la satisfactia acestora.
Implicarea si dezvoltarea angajatilor pentru a contribui la imbunatatirea continua a proceselor si a calitatii produselor oferite sunt alte componente esentiale ale managementului Lean. In filozofia Lean angajatii sunt incurajati sa participe la procesul decizional si sa propuna optimizari. Aceasta abordare joaca si un rol crucial in cresterea gradului de satisfactie a angajatilor, validandu-le contributia in succesul organizational.
Din punct de vedere operational, Lean prioritizeaza satisfactia clientilor prin livrarea prompta a produselor si serviciilor de inalta calitate, in cantitatile solicitate si la preturi competitive. Acest obiectiv este sustinut de adoptarea celor mai bune practici in eficientizarea operationala si dezvoltarea produselor, facilitand tranzitia organizatiilor de la dependenta de munca intensa la cresterea valorii prin inovare si organizare optima.
Ce beneficii ofera abordarea metodologiei Lean?
Lean ofera multiple beneficii care pot contribui la cresterea competitivitatii si succesului unei organizatii pe termen lung, printre care se numara:
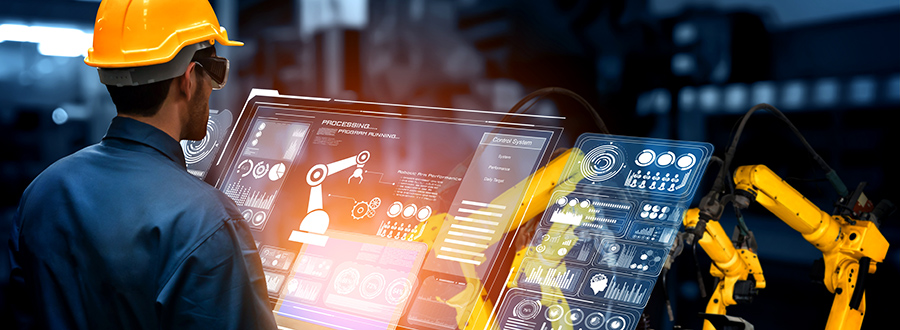
Care este rolul sistemelor software in implementarea principiilor Lean?
Solutiile software pentru productie sprijina principiile Lean in mai multe moduri. In primul rand, programele informatice sporesc vizibilitatea in intregul proces de productie, permitand identificarea si eliminarea risipei. Datele furnizate in timp real prin intermediul sistemelor software pentru productie pot ajuta la identificarea blocajelor, a ineficientei si a oportunitatilor de imbunatatire.
De asemenea, solutiile de automatizare pot urmari parametri de performanta in timp real, facilitand masurarea impactului schimbarilor si ajustarea strategiilor in functie de necesitati. Acest lucru se aliniaza indeaproape cu filozofia Kaizen, element cheie al productiei Lean.
Permitand procese de fabricatie mai agile si mai receptive, automatizarea sprijina principiul Lean de intelegere a perspectivei clientului. Prin valorificarea tehnologiilor digitale, producatorii pot raspunde mai rapid la cererile in schimbare ale clientilor, imbunatatind termenele de executie si satisfactia clientilor.
Sistemele MES si APS – instrumente cheie in implementarea filozofiei Lean Manufacturing
Solutiile de tip MES (Manufacturing Execution System) si APS (Advanced Planning and Scheduling) sustin filozofia Lean Manufacturing prin furnizarea de instrumente si functionalitati care optimizeaza procesele de productie si faciliteaza o mai buna gestionare a resurselor.
APS este o solutie software utilizata in companii pentru a sprijini procesele complexe de planificare si programare a productiei. Sistemul permite planificarea eficienta a resurselor, cum ar fi masinile, forta de munca si materialele. APS software ia in considerare diversi factori, precum capacitatile, disponibilitatea resurselor, termenele de executie, previziunile privind cererea si prioritatile pentru a crea un plan de productie optim. Prin utilizarea algoritmilor avansati, solutia APS ajuta la identificarea blocajelor, la reducerea timpilor de executie si la cresterea performantei in productie.
MES pentru managementul productiei, gestioneaza procesele de transformare a materiilor prime in produse finite, prin executarea comenzilor de lucru si monitorizarea eficienta a productiei si a datelor de control al calitatii pe multiple linii de produse sau chiar in diverse locatii. Prin capturarea si analiza datelor din diferite etape ale procesului de productie, MES ajuta la identificarea ineficientelor, a blocajelor si a oportunitatilor de imbunatatire. Aceasta abordare bazata pe date permite producatorilor sa ia decizii in cunostinta de cauza, sa implementeze actiuni corective si sa optimizeze procesele.
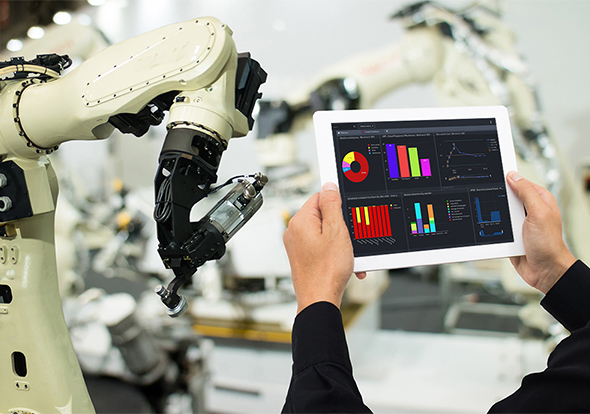
Afla cum poti avea control total asupra procesului de productie si al operatiunilor din fabrica!
Ai nevoie de mai multe informatii? Afla detalii de la consultantii Senior Software

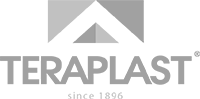
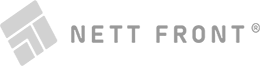
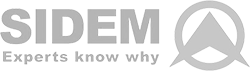
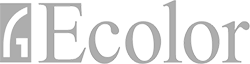
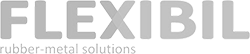